دانلود با لینک مستقیم و پر سرعت .
لینک دانلود و خرید پایین توضیحات
فرمت فایل word و قابل ویرایش و پرینت
تعداد صفحات: 162
مشخصات کلی کارخانه :
شرکت تولیدی بافت آزادی ( ساکای سابق ) سهامی عام در تاریخ 1384/03/06 تحت شماره ثبت 9228 در اداره ثبت شرکتهای تهران به منظور تولید و عرضه پارچه های کشباف ، تاری پودی بصورت رنگی و چاپی و انواع پرده های تور و فعالیتهای بازرگانی مرتبط با آنها به ثبت رسیده است و محل شرکت در بازار دالان امیدالملک و با ظرفیت تولید سالانه 400/000 متر انواع پرده ، توری و پارچه مبلی و دستکش بوده است . فعالیت اصلی شرکت طبق ماده 2 اساسنامه آن ایجاد و تاسیس و اداره کارخانجات تولیدی نخ ، بافندگی و تکمیل پارچه می باشد .
این شرکت در تاریخ 1356/01/25 به شرکت سهامی عام تبدیل و در تاریخ 1370/11/21 در سازمان بورس اوراق بهادار پذیرفته شده ( قبل از انقلاب اسلامی این شرکت ، یک شرکت خصوصی بوده است ) .
شرح درصد سهام
1) سازمان ملی گسترش مالکیت واحدهای تولیدی 36.51
2) شرکت سرمایه گذاری ملی ایران 9
3) خانواده سادات تهران 27.6
4) خانواده پورکاظمی 26.89
100
نحوه اداره شرکت پس از پیروزی انقلاب اسلامی :
اداره شرکت بافت آزادی پس از انقلاب اسلامی به استناد ماده واحد 6738 به عهده مدیریت دولتی قرار گرفت و در سال 1362 با توجه به زیان انباشته در اجرای ماده 141 قانون تجارت ، سرمایه شرکت از مبلغ 1/200/000/000 ریال به مبلغ 5/000/000 ریال تقلیل و در سال 1363 سرمایه شرکت از مبلغ 5/000/000 ریال به مبلغ 5/000/000/000 ریال افزایش یافت و در اسفند ماه همان سال در سازمان بورس و اوراق بهادار پذیرفته شد و سهام 54/97 درصد مربوط به سازمان صنایع ملی ایران در تاریخ 1374/04/12 در سازمان بورس و اوراق بهادار به کارگران شرکت و بخش خصوصی واگذار شد و به دلیل اینکه عملکرد شرکت از سال 1377 منجر به زیان گردیده ، معاملات سهام شرکت در سازمان بورس اوراق بهادار تهران به حالت تعلیق درآمده است .
ترکیب سهامداران درصد سهام
1) سازمان خصوصی سازی ( اصالتاً و وکالتاً ) 27
2) شرکت سرمایه گذاری ملی ایران 9
3) خانواده میراحمدی 28
4) کارگران و سهامداران دیگر 36
100
این شرکت دارای دو بخش جداگانه می باشد : 1) بافت (1) 2) بافت (2)
کارخانه بافت (1) دارای بخشهای چاپ تخت ، تکمیل ، تعمیرات شامل ، تراشکاری ، فرز کاری و… می باشد .
کارخانه بافت (2) دارای بخشهای گردباف ، کتن ، راسل ، وارپینگ ، ژاکارد ، برودری ( BRODERI) می باشد به علاوه قسمت چهارلاتابی ، سیستم اداره کننده هیات مدیره می باشد که تصمیمات اصلی توسط آن اتخاذ می شود کخ تحت نظارت این هیات مدیره ، مدیرعامل مسئولیت کارخانه ره به عهده دارد که در حال حاضر مدیرعامل جناب آقای قدکچیان می باشد .
بخشهای زیر ، زیر نظر مدیرعامل می باشد :
1) امورمالی و انبارها که شامل حسابداری و انبارداری است.
2) امور بازرگانی و تهیه مواد که امور مربوط به خرید و فروش و سفارشات کارخانه نیز می باشد .
3) امور اداری و کارگزینی
4) امور فنی و تولید که شامل آزمایشگاه ، بخش آمار و کنترل ، نگهداری و تعمیرات نیز می باشد .
5) بخش آموزشی که به آموزش کارگران و کارمندان اشتغال دارد .
همچنین کارخانجات بافت آزادی دارای شورای اسلامی کار می باشد ، که وظیفه آن دفاع از حقوق حقه کارگران و کارمندان و مرجع اختلاف کارگران و مسئولین می باشد .
کارخانجات بافت آزادی ( بافت (1) و بافت (2) ) بصورت مجزا اداره می شوند یعنی هر کارخانه بصورت مجزا دارای بخشهای اداری و کارگزینی و مدیریت جداگانه می باشد . مدیران هر قسمت زیر نظر مدیرعامل انجام وظیفه می کنند . انبارهای این کارخانجات شامل : انبار قطعات یدکی ، انبار پارچه خام ، انبار محصول ، انبار زائدات و انبار رنگ و مواد مصرفی می باشد .
در بخش بازرگانی ، تحویل سفارشات و فروش محصولات و بازاریابی جهت محصولات انجام می شود .
مواد مورد نیاز داخل کارخانه سعی می شود حدالمقدور از داخل کشور تهیه شود ، در غیر اینصورت از کشورهای خارجی تامین می شود .
کارخانجات بافت آزادی دو نوع محصول دارد :
1) بصورت سفارشات از شرکتها ، افراد حقوقی یا کارخانجات دیگر است .
2) محصولاتی که به سفارش خود شرکت می باشد که در فروشگاه بافت آزادی به فروش می رسد . این نوع سفارشات دربرگه های سفارش با شماره سفارشات مشخص تامین می گردد .
بخش مهم و حیاتی کارخانه که نقش بسزایی در سود دهی کارخانه دارد بخش آمار و کنترل کارخانه می باشد که کنترل و ثبت موارد در رابطه با تولید و انتقالات کالا دا به عهده دارد در این قسمت آمار تولید هر سال را بصورت مجزا حسابرسی کرده و سود حاصله را محاسبه می نماید و منحنی تولید و فروش هر سال را با سالهای قبل مقایسه می کند . در پایان لازم بذکر است که این کارخانه در کیلومتر 1 و 8 جاده کرج واقع شده است .
سالن وارپینگ :
این بخش از آنجایی که ابتدای کار است ، بسیار حائز اهمیت است زیرا اگر بی دقتی و خطایی در این بخش اتفاق افتد در بافت نیز مشکلات عدیده ای ایجاد خواهد شد .
دمای سالن cْ25 – 35 و رطوبت آن 75 – 85% می باشد .
بر اساس سفارشات سالن های راشل و کتن ، قرقرها را تهیه می کنند که بر اساس نوع بافت ، نوع نخ ، تعداد سرنخها و gauge ماشین متفاوت است . عمدتاً نخهای نایلون به شکل flat و نخهای پلی استر بصورت flat و تکسچره در اختیار این بخش قرار داده می شود .
عرض پارچه ها 4,3,2,1 متر می باشد .
طول هر قرقره 0.5 m می باشد که بر اساس عرض پارچه می توان از چند قرقره استفاده کرد . قرقره هایی که در یک شانه قرار می گیرند باید هم متراژ و یک اندازه باشند ، در غیر اینصورت نخ قرقره ای که اختلاف طول دارد ، ایجاد ضایعات می کند . عرض پارچه های راشل می تواند 2،3 و یا 4 متر باشد ، بنابراین ربای عرض 4 متر ، 8 قرقره ، برای عرض 3 متر ، 6 قرقره و برای عرض 2 متر 4 قرقره نیاز داریم که این قرقره ها باید هم متراژ باشند .
از آنجایی که gauge کتن بیشتر از gauge راشل است در نتیجه سرنخهای کتن بیشتر است . در کتن معمولاً 580 تا 720 رشته یا سرنخ پیشنهاد و سفارش داده می شود و در راشل معمولاً تعداد رشته ها 362 ،361،275 و … می باشد .
نخها پس از باز شدن از روی بوبین و عبور از سه ناحیه کشش مسیر زیر را تا پیچیده شدن روی بیم ها (پله) طی می کنند :
قفسه صفحه جداکننده شانه غلتک هدایت کننده شانه غلتک حاوی روغن شانه غلتک شانه شانه زاویه ای بیم (پله)
در این سالن 10 عدد ماشن warp داریم در هر کدام از آنها می توانیم از 600 بوبین استفاده کینم به جزء یکی از ماشینها که در قفسه آن تا 720 بوبین هم جا میگیرد . در این بخش پله پیچی بصورت مستقیم انجام می شود و نخها بصورت مستقیم از روی قفسه بر روی پله پیچیده می شوند .
برای قفسه های ماشین شمار 1،5 و 6 می توانیم از بوبین رزرو استفاده کنیم . در واقع برای همه قفسه هامی توانیم بوبین رزرو بگذاریم ولی گاهی اوقات شکل بوبین به گونه ای است که نمی توان برای آن بوبین رزرو گذاشت یعنی اندازه بوبین بزرگ است ، مثلاً بوبینهای 900 متری که به اندازه 3 بوبین 300 متری جواب می دهد احتیاجی به بوبین رزرو ندارد .
در هر دستگاه warp ، نخها بر روی دستگاه warp در قفسه ها سوار هستند و نخ روی راهنما قرار می گیرد که در اینجا کشش به نخ وارد می شود . همه فیلامنتها از قسمتی تحت عنوان پین عبور می کنند که در واقع فیلامنت بین دو صفحه ای قرار می گیرد که وزنی بر روی آن اعمال میکند که اگر بخواهیم وزنه را سبک کنیم روی سطح قرقره ناهمواری بوجود می آید .
در واقع برای ایجاد کشش و کشیدگی از یکسری پولکهایی استفاده می شود که وزنی را روی نخ اعمال می کند ، این پولکها نباید خشدار باشند زیرا نخ را زده دار می کند ، کثیف هم نباید باشند زیرا در این حالت بین دو پولک فاصله ایجاد شده و مانع ایجاد کشش لازم و کافی به نخ می گردد . اگر این کشش نباشد نخ شل وارد سیستم می گردد و در سطح قرقره ناهمواری ایجاد می شود که همین ناهمواری باعث فلامنت شکستگی و پرزدار شدن نخ می گردد . نخ از یکسری مسیرهایی که اصطلاحاً سرامیکی یا چینی می گویند عبور می کند . پس از عبور نخ از بین پولکها ، هر نخی از درون یکسری تابلوهای راهنما عبور می کند که از دورن تابلوی راهنمای اول 6 تار نخ عبور می کند . از روی تابلو دوم و سوم به ترتیب تعداد نخهای عبوری افزایش می یابد و در ادامه از تابلوی سوم به روی تابلوی مرکزی می رود .
در هر قفسه در جهت عمودی 12 تار نخ داریم که هر 12 تار بصورت یک رشته قرار می گیرد که پس از عبور از تابلوی مرکزی بصورت دسته ای توسط دو غلتک هدایت بصورت صفحه ای هدایت می شوند . در مسیر نخ شانه هایی داریم که از هر دندانه شانه یک نخ عبور می کند . (gauge آن بین 26 تا 28 می باشد) همه شانه ها باید تحت کنترل باشند . اگر شانه خشدار باشد یا شکسته باشد باعث فیلامنت پارگی و یا پرزدار شدن نخ می شوند .
عمده عیوبی که روی نخها وجود دارد ، پرز نخها می باشد ، به این منظور بعد از شانه اول وسیله ای بنام پرزگیر قرار دارد . برای از بین بردن این عیوب روی نخ به این ترتیب عمل می شود که کارگر پرز را گرفته و روی نخ گره می زند . اصول کار دستگاه پرزگیر بر اساس تغییر قطر نخ است . از ابزار دیگری که در مسیر نخ وجود دارد سرگیر است ، زمانیکه نخ پاره می شود ، یک سر نخ از قرقره کم می شود که در قسمتهای بعدی مشکل ایجاد می کند . کارگر سر نخ پاره شده را یافته و دوباره وارد قرقره می کند ، چرا که اگر قرقره به همین صورت پیچیده شود در قسمت بافت یک نخ کم می آید و در پارچه ایجاد زدگی می کند .
از آنجایی که نخ با قسمتهای مختلفی در تماس است دارای بار الکتریکی می شود . لذا قبل از اینکه نخ وارد قرقره شود باید بار الکتریکی آن تخلیه شود . (الیافی نظیر نایلون الکتریسیته ساکن پیدا می کند) برای این منظور یکسری ترانسهای داریم به شکل محفظه هایی استوانه ای شکل ، که ایجاد بار مثبت می کنند تا بار منفی را خنثی کنند . هر چه میزان بار مثبت بیشتر باشد ، بار منفی بیشتری از نخ تخلیه می گردد .
در مسیر عبور نخ ، غلتک روغن را داریم که از پارافین صنعتی استفاده می کنیم ، که میزان روغن را بر حسب میزان نیاز نخ تنظیم می کنند .
علل استفاده از غلتک روغن :
1) برای نرم کنندگی نخ
2) بعضی از نخها خشن هستند و تاب زیادی دارند و یا فیلامنت هایشان از هم باز می گردد که حالت چسبندگی را در آنها بوجود می آورد تا در هنگام بافت از هم باز نشوند که از این غلتکها بیشتر در مورد پلی استر استفاده می شود که جذب روغن بیشتری دارد . بعد از غلتک روغن ، نورد قرار دارد که وظیفه آن ثابت نگه داشتن سرعت خطی پیچش در طی مدت زمان پیچش می باشد و نورد بر اساس کششی که حس می کند با افزایش R قرقره میزان W را کاهش می دهد . سطح نورد باید کاملاً صاف باشد چرا که در اثر خشدار بودن می تواند ایجاد فیلامنت شکستگی کند .
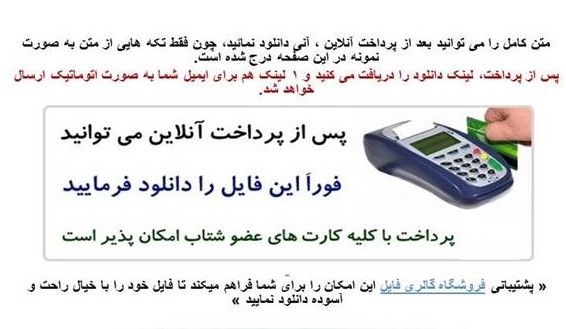